Problem Statement
How can a manufacturing unit effectively assess its capacity to fulfill new sales orders within specified timelines, ensuring accurate customer commitments and optimizing resource utilization?
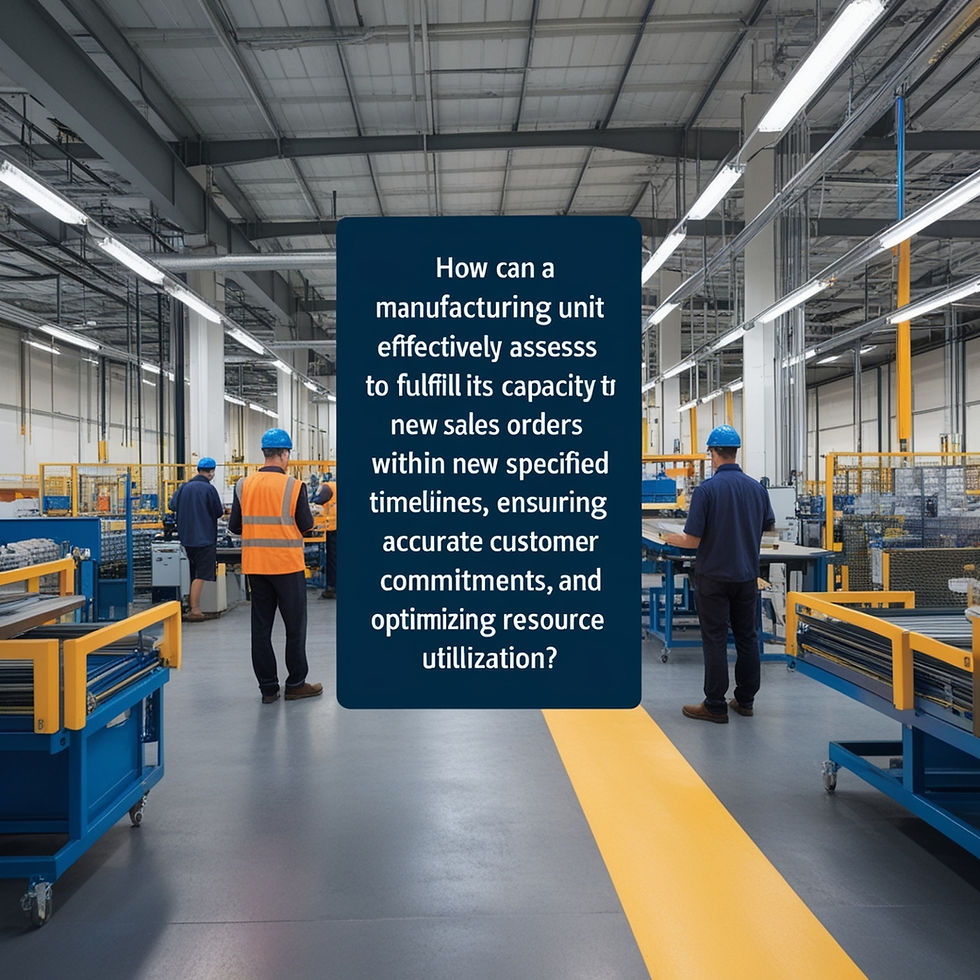
Introduction
In the dynamic world of manufacturing, accurate capacity planning is essential to avoid missed deadlines, overstocking, and underutilization of resources. ERPNext, a comprehensive open-source ERP solution, offers a robust framework for capacity planning. However, to ensure optimal efficiency and customer satisfaction, it's crucial to understand how to leverage ERPNext's capabilities effectively.
Key Elements of Capacity Planning in ERPNext
Bill of Materials (BoM) with Operations and Time:
Define detailed operations required for each product, including the time needed for each operation.
This information is crucial for calculating production time and resource allocation.
Workstations and Production Capacity:
Specify the production capacity of each workstation, indicating how many operations can be performed simultaneously.
Define working hours and holiday lists to accurately account for available production time.
Routing:
Establish the sequence of operations for each product, ensuring that subsequent operations can only begin after the preceding ones are completed.
This prevents bottlenecks and delays in the production process.
Job Cards and Time Management:
ERPNext automatically generates job cards based on work orders, providing a clear overview of tasks and deadlines.
The system warns of overlapping job card times, preventing conflicts and ensuring efficient resource allocation.
Calculating Production Capacity
To assess your production capacity, use the following formula:
Production Capacity = Total Working Hours per day / Total Operational Time required to produce each Item.
Note: Total Working Hours can be derived as defined in each Workstation. Total Operational Time required to produce each Item is defined in BoM.
This calculation helps determine how many units can be produced in a day. But this calculation is not available by default and needs to be customized in Frappe.
Understanding Stock Projected Quantity
Purpose: To provide a clear and accurate forecast of available stock units based on various factors.
Calculation: The projected quantity is determined using the following formula:
Projected Quantity = Actual Quantity + Planned Quantity + Requested Quantity + Ordered Quantity (Purchase Order) - Reserved Quantity (Sales Order) - Reserved Quantity (Production) - Reserved Quantity (Subcontracting) - Reserved Quantity (Production Plan)
Availability: To determine when the projected quantity will be available for fulfilling new sales orders, consider factors such as:
Production capacity: The rate at which your facility can produce units.
Lead times: The time required to procure materials, manufacture products, and complete other necessary steps.
Demand: The expected rate of sales or usage of the product.
Customization: A customized report can provide more specific insights by incorporating additional factors, such as:
Expected delivery dates: For purchased items.
Production schedules: To track the progress of in-house manufacturing.
Inventory turnover rates: To assess how quickly stock is depleted.
Benefits: By understanding the projected quantity and its availability, businesses can:
Optimize inventory levels: Avoid stockouts or excess inventory.
Improve production planning: Ensure sufficient capacity to meet demand.
Enhance customer service: Fulfill orders promptly and accurately.
Make informed purchasing decisions: Procure materials at the right time and in the right quantities.
Would you like to explore any of these points further, or do you have other questions about stock projection?
Written by - Hemant Asaldekar
Comments